Wilanów Cabinet
Automated stage for high resolution 3D scanning of large surfaces for cultural heritage documentation.
Goal of the project
The aim of the project was to 3D scan the surface of the walls and ceiling of historical Kings Chinese Cabinet at Museum of King Jan III’s Palace at Wilanów. Required resolution and accuracy was set at high level of 100 points per square millimeter with accuracy of 30um. Such high accuracy implies us to use structured light projection scanning method with limited measurement volume. With the dimensions of scanned room of 4x4x5 meters, more than 100 square meters of scanning area, we need to take thousands of scans. The acquisition and management of such a large amount of data, aligning scans and building the final 3D model was a big challenge.
Idea for measurement setup
For efficient digitization of historical interiors like Kings Chinese Cabinet system must comply with several requirements. First, with thousands of positions required, the measurement head should be positioned in automatic way. This will significantly speed-up the data acquisition step. Second, scans should be roughly aligned just after the acquisition. Another challenge was due to the fact, that the room is over 5 meters high. Scanner head to measurement volume distance is approx. 75cm, that means that we must lift measurement head 5 meters above the ground to capture the top-most parts of the room. Whole construction should be stable, rigid and safe. Measured objects are priceless, there is no room for error. Used system consists of the motorized vertical column with robotic arm (Fanuc LRMate 200i of 700 mm range), that holds 3D measurement head. Column is placed on a wheeled platform, which allows the free movement of the structure inside the Cabinet. Vertical column is high enough to reach the top-most parts of the Cabinet ceiling. Finally, whole construction should be stable, rigid and safe. Measured objects are priceless, there is no room for error.

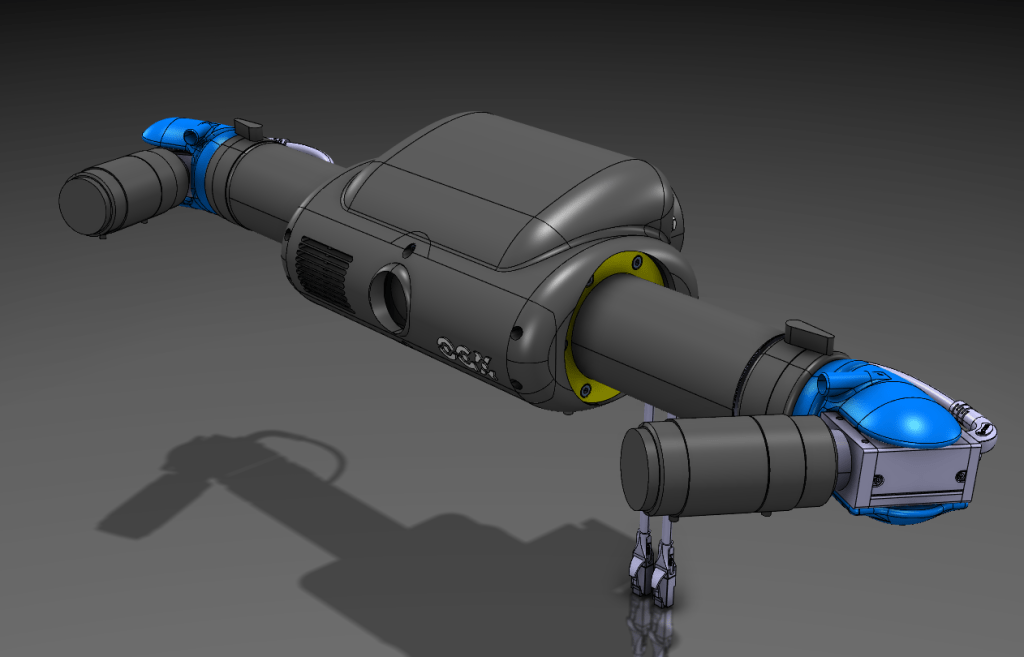
Fig. Measurement setup – concept
Measurement head
To meet conservators’ requirements (measuring surfaces with light-sensitive pigments) no ultraviolet nor infrared radiation emission in the direction of measured object is allowed. We decided to use commercially available DLP Optoma projector with LED light source. Measurement head uses 2 cameras 9 Mega Pixel cameras on both sides of the projector, observing the same measurement area. That helps us to scan shiny parts of the object. In most cases, if the specular reflection is visible with one camera, the same part should be well-measured with the second one. Additionally, head should be lighter than 5kg so it can be easily lifted by robotic arm. 3D printing technology and carbon fiber parts were used to build a final version of the device. The device used the calibration method described in [3], which allowed to achieve a working volume of size 200x280x200mm and resolution of 0.1 mm, measured as the average distance between points in the captured cloud.
Additional lightning equipment
Stitching final 3D model from separate scans, each one captured with different scanner-head position results in non-uniform color of final model. Additionally, some specific parts of Kings Chinese Cabinet ere extremely shiny, resulting in unpleasant highlights visible on final model. To achieve uniform brightness for model we should use shadow-less lighting system, not moving during the whole digitization process. That is impossible due to lack of space and system self-shadowing resulting from limited 3D-scanner to measurement volume distance. To resolve this problem, we capture images with few additional lights and run complex color-correction procedure at model post-processing stage. 6 LED light sources are used to capture additional images. 2 smaller LED panels are attached directly to the scanner head next to cameras. Position of these 2 light changes with cameras and DLP projector. 4 bigger panels are attached directly to the lift of vertical column and are arranged in square layout with dimensions 1,2×1,2m. Bigger lights are further than 2m meters from the currently measured surface and move only when the level of vertical column is changed. These 4 lights can produce constant lightning conditions for all are measurements captured in the single platform position, except when robot arm obscures individual panels. All lights produce soft, diffuse daylight with color temperature of 5650K. Additionally, smaller panels are certified for ability of faithful color reproduction of illuminated objects with CRI Ra>95.


Fig. Measurement setup – the final design
Data acquisition & processing path
Table below shows approximately the number of scans required to cover the whole area of Cabinets walls and ceiling. With measurement volume of single scan of 200x280x200mm and 50% overlap between consecutive scans, more than 12000 scans were captured from 6000 separate head positions.
consecutive platform positions | 50 | |
vertical column different positions (3 levels for each platform position) | 150 | |
different measurement head positions | automatic sequence (25 per column level) | 3750 |
semi-automatic additional measurements (approx. 15 per column level) | 2250 | |
TOTAL number of scans | 12000 |
At single platform position, robot arm is lifted at 3 different levels above the ground. On each level operator starts automatic sequence with 25 different scanning-head positions, covering area of approx. 0,8×0,8m. When automatic sequence completes, we can start with semi-automatic measurements of parts with more complex shape, where defects appeared. Using the next-best view algorithm described in operator just must point the area where next scan should be performed. If calculated measurement head position is reachable, robotic arm starts movement. Scan starts immediately after reaching requested position. When the lower part of the Cabinet was finally measured, vertical column was extended and the process was repeated for upper-part and ceiling of the Cabinet. Images acquisition takes approx. 20 seconds. With additional time for calculation of point cloud, saving data, next-best view procedure and robot movement, next measurement can be performed after approximately 3 minutes. Two scans are captured and calculated simultaneously, for both left and right detector. Finally, the process of scanning the whole Cabinet last 8 weeks, with approximately 350 scans per day.
We invite you to watch the movie (polish version only), which is a summary of the work carried out during the project:
More details about restoration works of Cabinet can be read on the pages of the Museum of King Jan III’s Palace at Wilanów
http://wilanow-palac.pl/prace_konserwatorskie_w_gabinecie_chinskim_krola.html